Technical


TECHNOLOGY & MANUFACTURE
Filament winding technology enables the strength of glass fiber to be distributed in the required directions, optimizing the best use of the orthotropic nature of the composite material system. In addition to the strength, glass fiber composite is four times lighter than steel for the same strength and hence these pipes have very high specific strength. The corrosion resistance of GRP pipes is the result of using various resins like polyester, vinylester, epoxy etc., Since the pipes are built layer-by-layer using glass filament as reinforcement and resin as the matrix, it is possible to offer a vast range of properties designed for specific applications.
SSC’s latest composites technology delivers a custom built GRP Pipe, utilizing optimum design and based on the most appropriate resin for the service, which results in long life and very cost effective. GRP pipes are manufactured by SSC by the Dual- Helical winging process.
DESIGN PHILOSOPHY
SSC is totally committed to designing the most optimum and cost effective GRP piping system. It specializes in complete piping solution for a given application and site conditions. SSC will conceive and propose an appropriate piping system based on the customer’s project requirement.
A number of parameters are involved in GRP piping system design. The experience of the designers plays a vital role in providing an optimum piping solution. It is this aspect where SSC adds value to the clients.
Design Methodology
I. SELECTION OF RESIN SYSTEM:
The most appropriate resin system is selected based on the fluid to be handled.
II. JOINING SYSTEM:
The jointing system is decided based on the pressure rating and the installation conditions. Typically, the underground piping system has push-fit type joints wth Bell and Spigot or Double-bell coupler type joints.. Specials like bends and tees are jointed to the pipeline by push-fitting or butt & wrap type joints. Above ground pipes are fixed with key-locked push-fit type, butt & wrap, adhesive or flanges.
Resin Systems:
- Isophthalic Polyester
- Vinylester
- Superior Vinyl (Novolac) ester
- Vinylester for corrosion barrier and Isophthalic Polyester for structure
- Superior Vinylester for corrosion barrier and Vinyester for structure
- Aliphatic amine cured epoxy
- Aromatic amine cured epoxy
Codes & Standards
The following Codes and Standards are applied by SSC during manufacturing, testing and installation of GRP pipes
Standard | Description |
---|---|
ANSI/AWWA C-950 | Standard for Fiberglass Pressure Pipe |
ASTM D2310 | Standard Classification for Machine-Made Reinforced Thermosetting-Resin pipe |
ASTM D2996 | Standard Specification for Filament –Wound “Fiberglass” (Glass Fibre Reinforced Thermosetting-Resin) Pipe |
ASTM D3262 | Standard Specification for “Fiberglass” (Glass-Fiber-Reinforced Thermosetting-Resin) Sewer Pipe |
ASTM D3517 | Standard Specification for “Fiberglass” (Glass-Fiber –Reinforced Thermosetting-Resin) pressure Pipe |
ASTM D3754 | Standard Specification for “Fiberglass” (Glass-Fiber-Reinforced Thermosetting-Resin) Sewer and Industrial Pressure pipe. |
ASTM D4161 | Standard Specification for “Fiberglass” (Glass-Fiber-Reinforced Thermosetting-Resin) Pipe Joints Using Flexible Elastomeric Seals |
BS 5480-90 | British Standard Specification for Glass reinforced plastics (GRP) pipes, joints and fittings for use for water supply or sewerage. |
BS 7159 -89 | Design and construction of glass reinforced plastics (GRP) piping systems for individual plants or sites. |
Testing Procedures
SSC applies internationally accepted test procedures with the latest testing machines and expert personnel. QA/QC is key aspect of this professional company.
I. Production Testing:
Each and every pipe is tested for the following:
- Visual inspection (ASTM D2563)
- Resin cure by Barcol hardness
- Dimensional Check for Wall thickness, Length & Diameter (ASTM 3567)
- Hydrostatic leak tightness test to twice rated pressure (AWWA C950)
II. Batch Testing:
One pipe in every 100 pipes or lot size as specified by the customer is subjected to the following test:
- Hoop tensile strength (ASTM D 2290)
- Axial tensile strength (ASTM D2105/D638)
- Stiffness & Flexural Modulus (ASTM D 2412)
- Structural integrity at deflected condition (ASTM 2412)
III. Type Testing:
Pipes manufactured with new resin systems or a new project is subjected to the4 following rests:
- Long Term Strength – Hydrostatic Design Basis (ASTM) D 2992)
- Strain Corrosion (ASTM D 3681)
- Long Term Ring –Bending (ASTM 5365)
- Impact Resistance (BS 5480)
- Short term rupture (ASTM D 1599)
- Pipe Joints Using Flexible Elastomeric Seals (ASTM D 4161)
Product Range
SSC offers a wide range of piping products of various resin system and jointing options:
Diameter : 1 inch to 160 inches ( 25mm to 4000 mm)
Custom diameters can be manufactured
Jointing systems: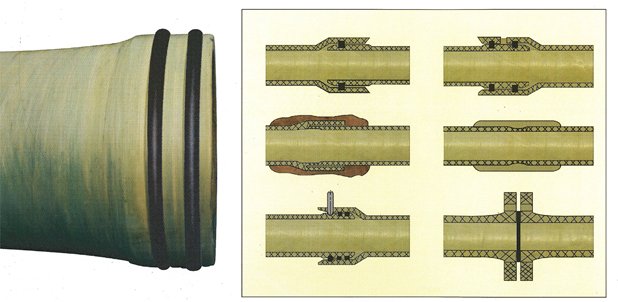
a) Restrained type:
- Butt & Wrap
- Flanged
- Bell & Spigot
- Adhesive Joints with Bell & Spigot (Tapered and Straight)
b) Unrestrained type:
- Bell & Spigot with elastomeric rubber seal (“ O” ring or “Reka” ring)
- Double-bell with elastomeric rubber seal (“O” ring or “Reka” ring)